PETI®-330(development product)
Overview
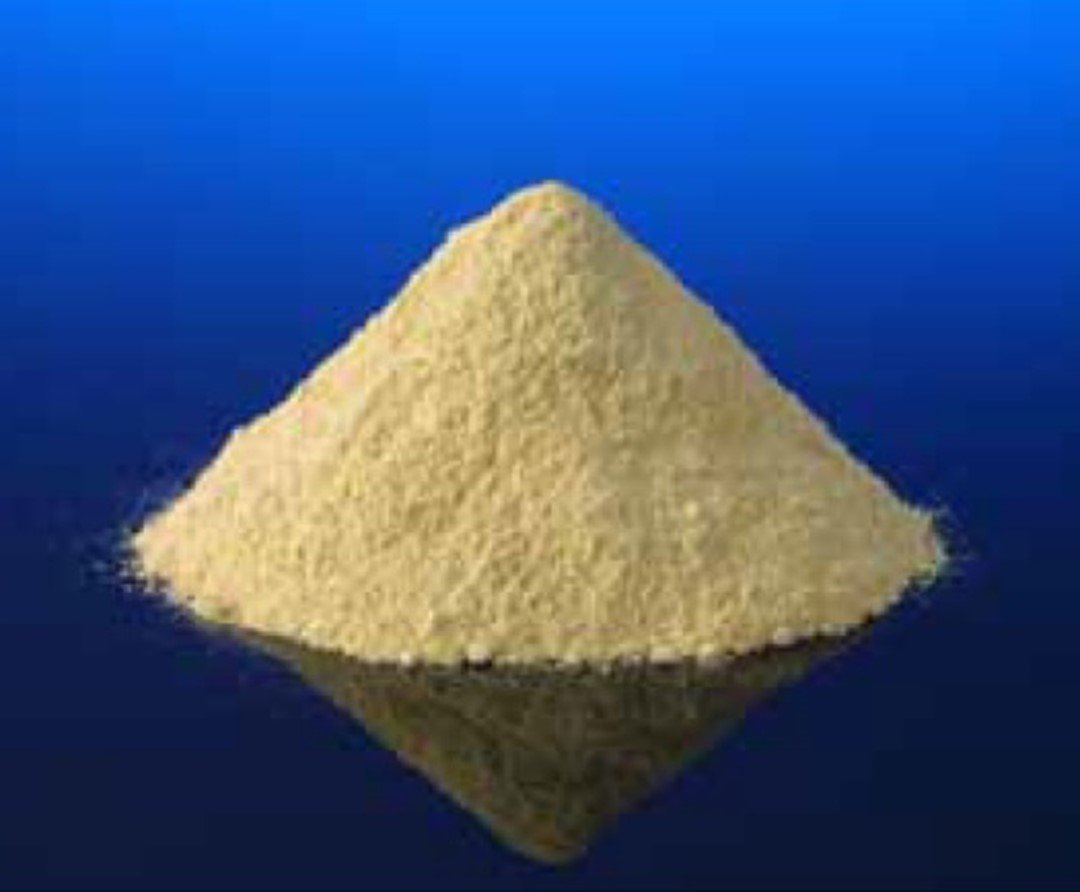
It is an imide oligomer with addition polymerization terminals, and can be used as a matrix resin for high-concentration filling of highly heat-resistant composite materials and various fillers.
There is no need to use a hardening agent, and it can be cured using only resin.
Features
-
1.Ideal for RTM molding
Melts at 200℃, has a low viscosity of 2Pa・sec and is stable for a long time.
-
2.Combines heat resistance and mechanical properties
The glass transition temperature of the cured resin is as high as 330℃
Highest level among resins -
3.Environmentally friendly
Lighter weight of high heat-resistant structural parts (substitute for metal parts)
Improved heat resistance and longer life of various parts
- #high heat resistance
- #matrix resin
- #high heat resistant composite material
Applications
-
Aircraft parts/industrial machinery parts
-
Diamond tools/
Friction materials/sliding parts
Manufacturing Methods
-
Molding conditions by RTM
1.Put PETI-330 into the injector, melt it at 280℃, and vacuum degas it for about 1 hour.
2.Set reinforcing fibers such as carbon fiber (CF) into the mold.
(If necessary, perform vacuum heating at 400℃ for about 2 hours to remove the CF sizing agent)
3.The temperature of the mold is maintained at 300℃, and molten and degassed PETI-330 is injected.
The injection pressure is approximately 1.34MPa.
4.After injecting PETI-330, raise the mold temperature to 370℃ and cure at 370℃ for 1 hour.
5.After curing is complete, the mold temperature is cooled to 100℃ and the product is removed.
(Mold clamping pressure is maintained until the product is removed)
Furthermore, in order to improve heat resistance, it is heated to 360~370℃ in an oven.
We recommend post-curing for 6 hours.
It can also be molded using hot press.