What is nylon?
Engineering Plastics
Nylon serves a wide range of applications with its very good balance of properties, even compared to other engineering plastics. Here is a look at the characteristics, advantages, and uses of a material whose market promises to continue growing in the years ahead.
Overview
Nylon (polyamides) is a family of engineering plastics
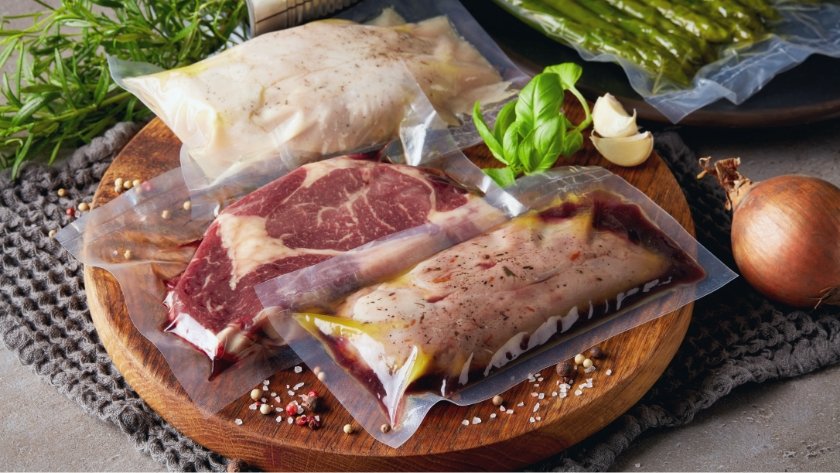
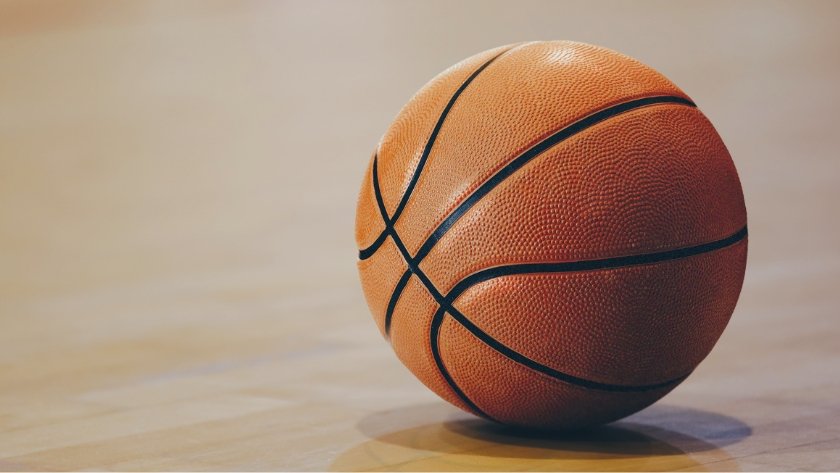
Say the chemical name "polyamides," and most people will draw a blank. Tell them the common name "nylon," and they'll immediately recognize the material that pervades our everyday lives. As one family of engineering plastics--plastics developed to provide greater strength and heat resistance--nylon is designed to better withstand high temperatures, overcoming a drawback of standard plastics. It is a high-performance polymer that offers diverse outstanding properties.
These polyamides come in many types and are versatile materials that are durable, resist heat, and can be shaped into many different forms. They are used in all sorts of products that make our lives better, including the plastic films that wrap the meat and fish sold at grocery stores, sporting goods such as basketballs and sneakers, automotive parts requiring superior durability, consumer electronics, clothing, everyday necessities, and toys.
Features
A magic material adaptable to many uses
Compared with other engineering plastics, polyamides are easy to process and offer high reliability and a good balance of properties, making them suitable for diverse applications. However, in almost all cases, polyamides are not used as is. Instead, they are blended with various agents--the choice depending on the functions or properties needed in the finished product--and the resulting compound is pelletized. Because of polyamides' broad affinity, they can be freely blended with a wide range of agents, such as additives (antioxidants, UV absorbers, antistatic agents, etc.), colorants (dyes and pigments), stiffeners (glass fibers, carbon fibers, etc.), and fillers. This means that nylon can be used to meet various purposes in materials.
For example, nylon is well known as a useful material for clothing because it strongly resists abrasion and wrinkling, and does not attract insect pests. Less known is the fact that polyamides are used in parts surrounding automobile engines and in products requiring electrical insulation.
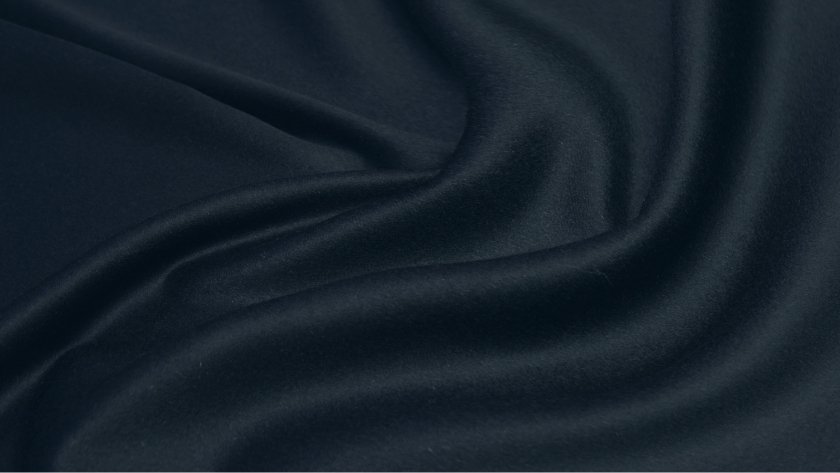
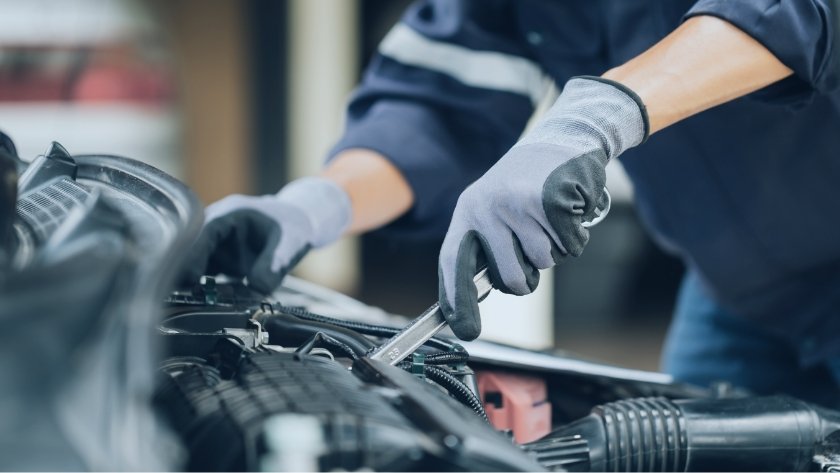
Made using a unique process, UBE Nylon solves diverse challenges!
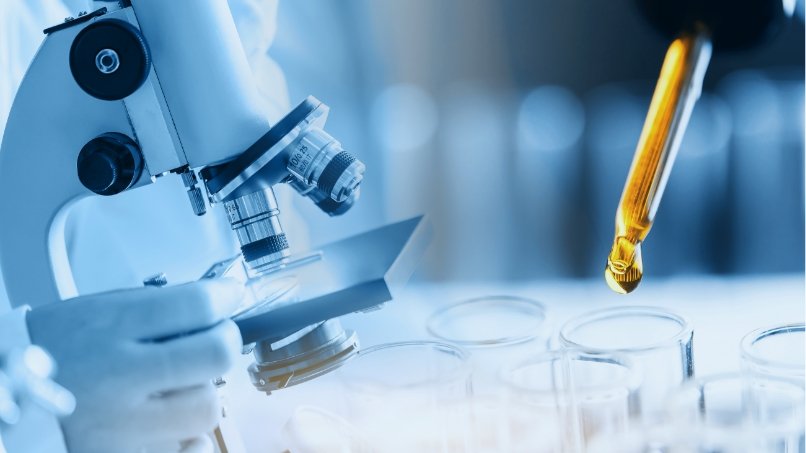
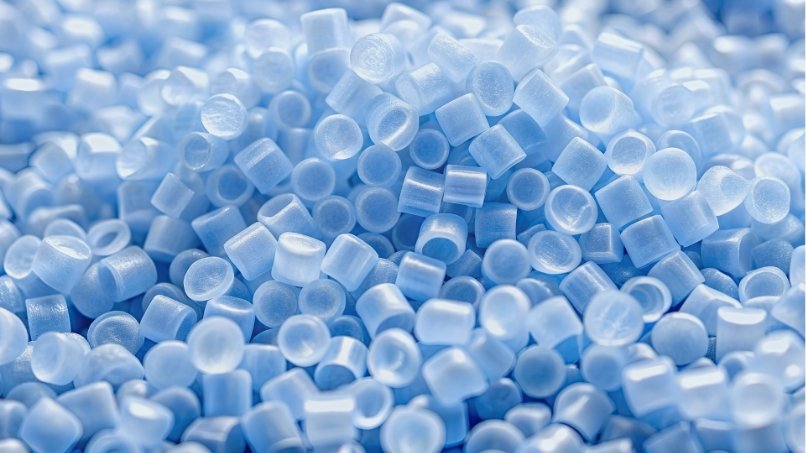
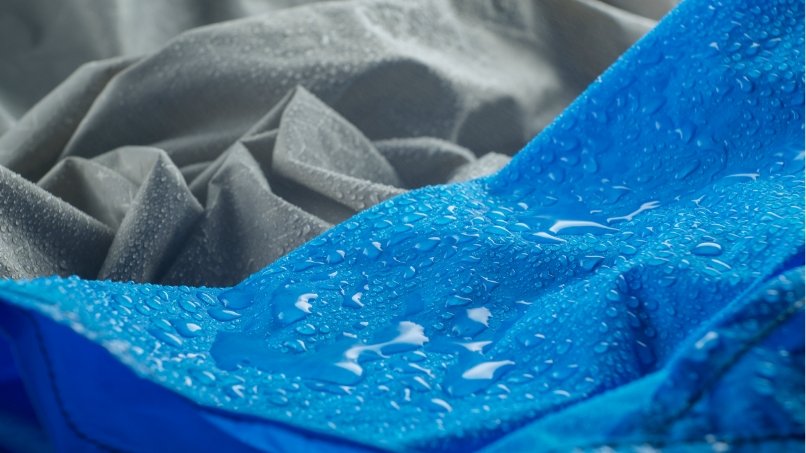
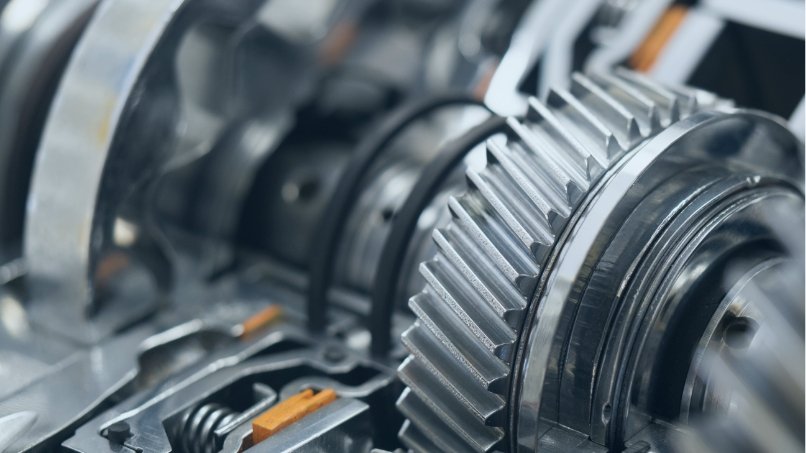
Of the many types of nylon available, three of the more widely used forms are Nylon 6 (PA6), Nylon 66 (PA66), and Nylon 12 (PA12). Nylon 6 offers outstanding durability (strength) and heat resistance, and Nylon 66 provides even greater heat resistance and mechanical strength. Because of those characteristics, these two exemplary polyamides are used in diverse products broadly ranging from apparel to industrial-purpose items, and even serve as a metal substitute in some industrial applications.
Nylon 12 has the lowest density of all polyamides. It has earned a global reputation for the ability to solve many challenges with its high quality and superb cold impact resistance and weather resistance. It especially stands apart from other polyamides for its superior performance at low temperatures. We produce UBE Nylon 12 (UBE Nylon PA12) using a unique polymerization process that ensures the quality and stable physical properties of this nylon, whether as pellets or finished products. It offers the following advantages.
1.Lower water absorption with excellent dimensional stability
2.Excellent performance at low temperature
3.Superior impact resistance
4.Excellent processability, thus suitable for molding complexly shaped parts
5.Superior weather resistance
6.Excellent adherence with metals
We also offer UBEST XPA, a polyamide elastomer based on Ube Nylon 12. In addition to delivering the same characteristics of Nylon 12, this material realizes a level of flexibility for improving compatibility between plastic and rubber, and achieves superior transparency and quality. Its ability to solve various challenges with those advantages has made it a popular choice for customers worldwide.
History
A look at UBE Nylon and its over 50 years of history
UBE leverages unique monomeric precursors to produce diverse nylons based on Nylon 6 (PA6) and Nylon 12 (PA12). UBE Nylon's distinctive strength lies in our ability to maintain stable quality and productivity through in-house manufacturing, and our technical expertise for meeting the functional needs of customers.
Our over 50 years of experience in this field has made UBE Nylon a trusted brand across the globe.
Over 50 years of history have made UBE Nylon a trusted brand worldwide
- 1959
- Completion and launch of Nylon 6 polymerization plant at UBE Chemical Factory
- 1977
- Completion of Nylon 12 pilot plant at UBE Chemical Factory
- 1979
- Completion and launch of Nylon 12 polymerization plant at UBE Chemical Factory
- 1995
- Establishment of UBE Nylon (Thailand) Ltd. (UNL, subsidiary in Thailand)
- 2001
- Establishment of UBE Engineering Plastics, S.A. (UEP, subsidiary in EU)
- 2002
- Completion and launch of nylon compound plant in Thailand
- 2004
- Completion and launch of Nylon 6 polymerization plant in Spain
- 2010
- Completion and launch of Nylon 6 polymerization plant expansion in Thailand
- 2012
- Completion and launch of nylon compound plant expansion in Thailand
- 2015
- Completion and launch of Nylon 6 polymerization plant expansion in Spain
- 2017
- Completion and launch of nylon compound plant expansion in Spain
- 2018
- Completion and launch of Nylon 6 polymerization plant expansion in Spain
Applications
Nylon-based products protect us and enrich our lives
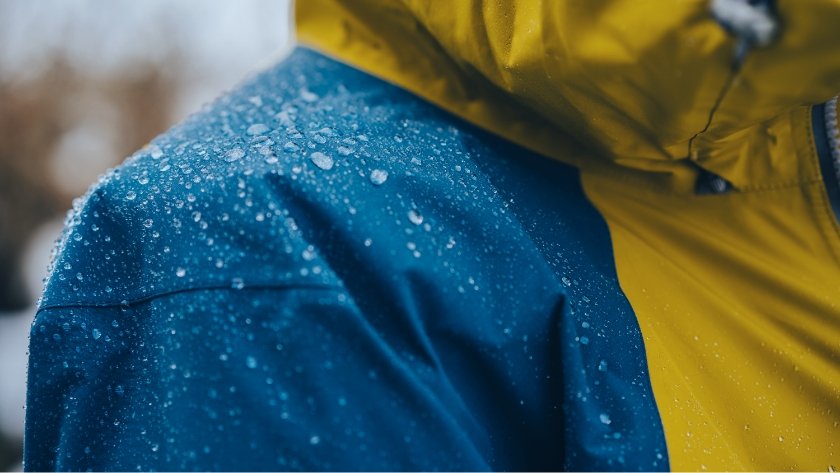
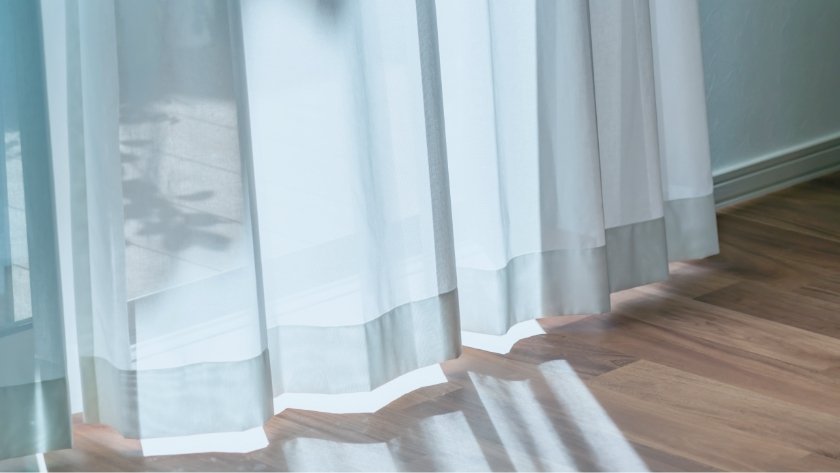
The ability to combine nylon with various agents allows diverse improvements to be made to materials. For example, antioxidants that prevent heat-related deterioration can be added to nylon for products used in hot conditions for a long period of time. Also, UV absorbers can be blended with nylon to prevent discoloration and cracking of plastic products used outdoors for leisure or other purposes. Nylon pellets incorporating reinforcing fibers that increase durability (strength) and elasticity are used in various products that make our lives more comfortable.
Enhanced nylon materials also help protect our bodies through their use in rainwear, jackets, sportswear, sneakers, and other shoes. They also improve the durability, safety, reliability, and beauty of interior products such as carpets, furniture and curtains. Everyday life is enriched by the many products that utilize nylon, including fashion accessories, shoes, outdoor gear, product packaging, fishing lines and nets, and musical strings.
UBE nylon films are found in every corner of our lives
Our UBE Nylon offerings serve a wide variety of applications in products ranging from apparel to industrial-purpose items. They are available in many different forms, including fibers, films, sheets, pipes, panels, round bars, and tubes. Nylon films in particular are a very versatile material. The films we produce are primarily extruded and co-extruded films.
Our extruded films are widely used in packaging for food, machine parts, and other products, owing to advantages such as their superior oxygen barrier function and strong resistance to rupturing, puncturing, and pinholing. These films are used to make three-side seal pouches for holding the soup of instant ramen, pillow pouches for rice balls, sweet buns, and frozen food, capped pouches for shampoo, fabric softeners, jelly drinks, soy sauce, and other condiments, as well as retort pouches. They are also employed in vacuum insulation for lithium-ion batteries and refrigerators.
Meanwhile, co-extruded films resist cracking, even when repeatedly folded, and have excellent sealing and oxygen/steam barrier properties. This makes them highly suited for applications such as meat packaging. In particular, they are used as shrink films and deep-draw films for packaging ham or sausages, as well as sausage casings and liquid pouches such as those used in wine boxes.
In every corner of your life you'll find UBE Nylon.
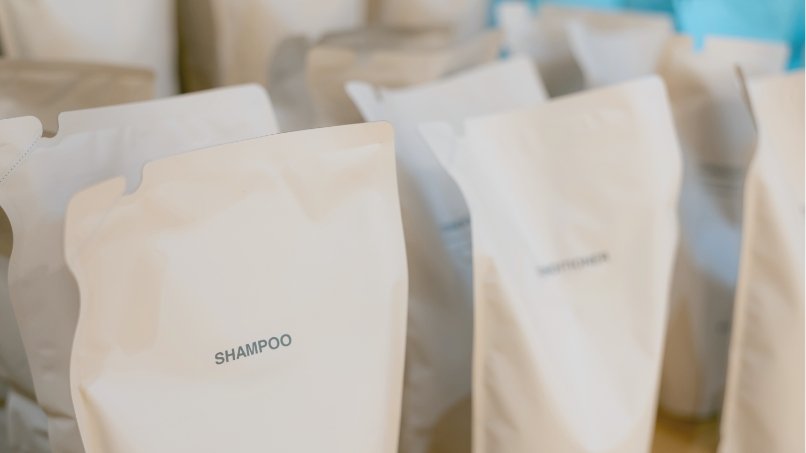
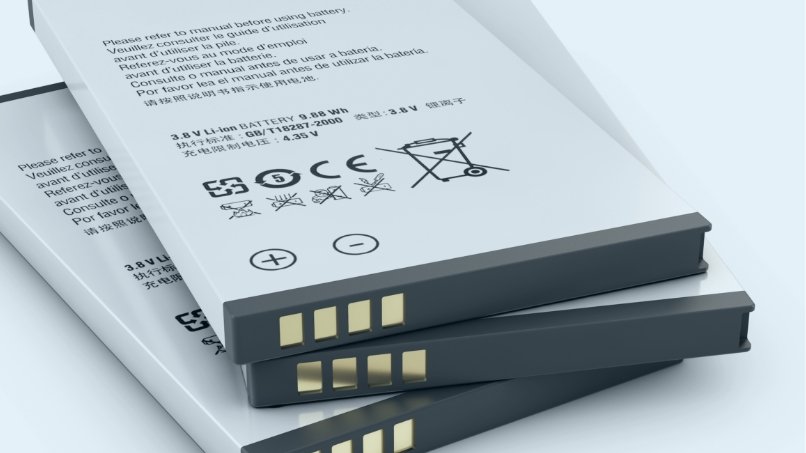
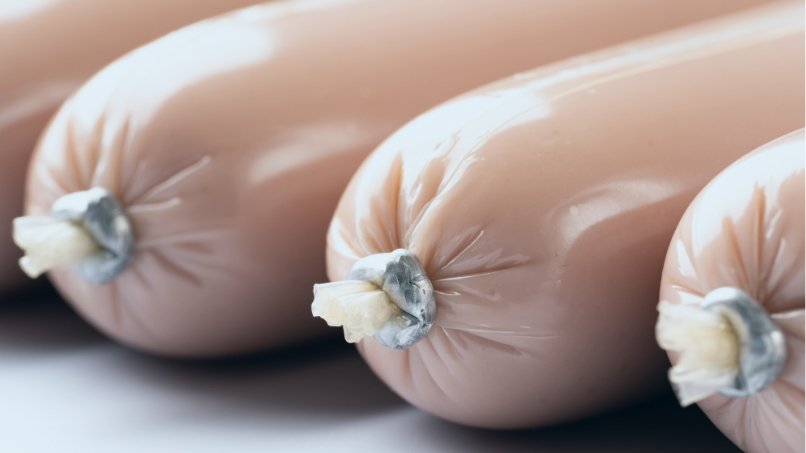